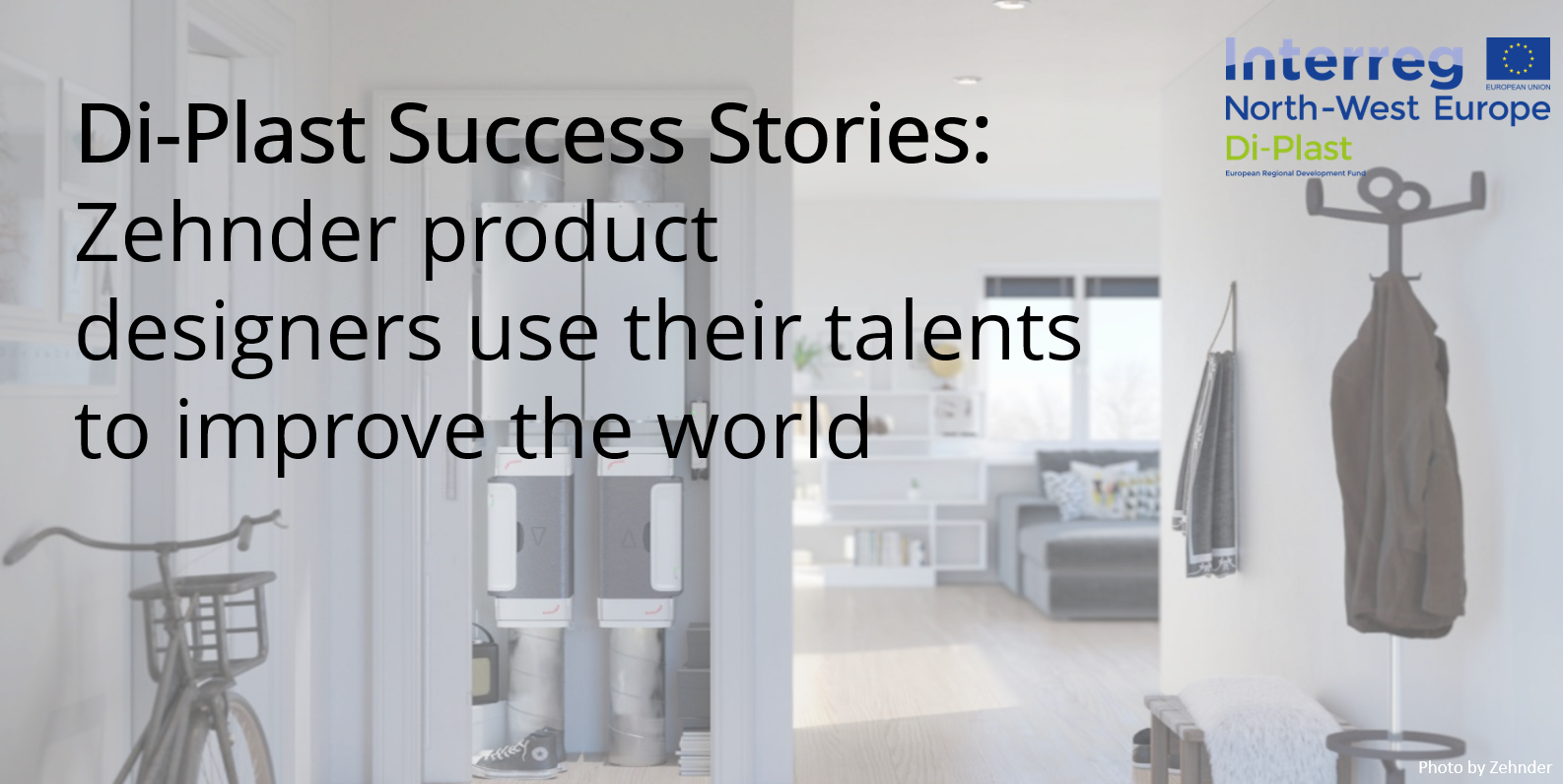
Product designers largely determine a company’s carbon footprint. The things they come up with are produced on a large scale and recycled if all goes well. Koen Korterik and Rogier Lansink are industrial product designers at Zehnder, a producer of systems for heating, cooling, ventilation, and filtration. Everything you need for a healthy indoor climate, in other words. The product designers are now looking into making a more sustainable mechanical central extraction system with the help of a Di-Plast subsidy.
“Technicians always want to learn: what is already possible, how can technology improve products, and what else is possible?” says Korterik enthusiastically. “There are a thousand ways in which something will not work and only a few in which it will. Our job is to find those ways.”
Lansink is ready to start. His challenge is to find a way to make mechanical central extraction systems, a decades-old system, from 95 percent recycled plastic. This is one of the changes that can make the device more sustainable. Others are a motor fan that lasts longer, cardboard packaging and using parts that can be transported and replaced as modules. “I will start with the housing of the extraction system. It isn’t an odd shape; we should be able to make it out of recycled plastic without much trouble. However”, he says, “it still has to work.”
This refers to the first “hurdle” that Zehnder has to overcome. “We normally add a raw material to virgin plastic to make the material solid. Talc, for example. But adding such raw materials makes it more difficult to recycle. So, you guessed it, we will not use these additives for recycled plastic, and the plastic will be more flexible”, explains Koen. “This makes it possible for air to leak through, which does not improve the product’s effectiveness. We already make the lid of the extraction system out of recyclate. We were able to guarantee dimensional stability by using ribs to give the lid the necessary sturdiness.”
120.000 kilos less virgin plastic
Zehnder received a Di-Plast subsidy at the start of 2022. This INTERREG project aims to have just under 100 companies in East Netherlands cooperate in the new plastic cycle and recycle over 100,000 tons more plastic. The expectation is that Zehnder can make a significant contribution to this. Lansink makes a short calculation: “This extraction system weighs over 2 kilograms, and we produce around 50,000 per year. That means that we have the potential to replace at least 120,000 kilos of virgin plastic – made from petroleum – with recycled plastic. That is a couple of truckloads. And, not to mention, we can use the knowledge we gain here on other Zehnder products.
Using talent for the world
The €5,000 subsidy incentivizes Zehnder to zoom in on one product and make it more sustainable, but the two product designers have a ‘drive’ to work with recycled materials either way. “The market demands it because of raw material scarcity and the need for cost savings, among other things, but we also want to contribute to the world,” says Korterik. “I used to work at a central heating manufacturer. My job was fun, but I was not too fond of the environmental impact of burning natural gas. I wanted to use my talents for something that would improve the world. We work on cleaning air at Zehnder, and we have the opportunity to make products more sustainable. We even have a ‘sustainability guild’ within the company, which focuses on minimizing negative environmental impact.”
Big results with limited effort
Minimizing environmental impact is the starting point of Rogier’s Di-Plast project. “We found that 75 percent of our portfolio can be easily made recyclable. The other 25 percent is more difficult. We will focus on the 75 percent first to achieve the greatest result with the least effort.”
Compromise
Koen and Rogier have internal support to reach their goal. “Our product marketer sees the need for a smaller ‘footprint’. He dares to compromise, which is necessary: recyclate is a bit less smooth and less bright in color, for example. He will say it is too bad because the product is now future-proof.” Koen expects that a second part of the extraction system can be made with recyclate in the course of 2023.
Injection molding plant is eager
Zehnder is using the Di-Plast subsidy to collaborate with a consultancy. “This consultancy has a lot of experience working with recycled materials. We have already learned a lot”, says Rogier. “One of these things is that we must first list the quality requirements of the product. For example, we need to consider the product’s shape and appearance. And we have also learned that we must gradually increase the percentage of recycled materials. This means that successive batches of products will have 10, then 20, then 30 percent recycled materials, and so on, until we have reached 95 percent recyclate. This allows us to properly monitor the deviations that changing the composition can cause. The goal is 95 percent instead of 100 percent because recycled plastic does not work ‘nicely’ for injection molding plants. The ‘melt flow rate index’ is less favorable. Processors need to apply more pressure to get the material to flow anyway. They also have more work cleaning the molds because leftover materials remain in them.” The injection molding plant with which Zehnder works is still eager to become more sustainable, though. “They do not mind working with less flexible materials; they also want to do well for the environment. And anyone who wants to continue making plastic products has to do so in a responsible way.”